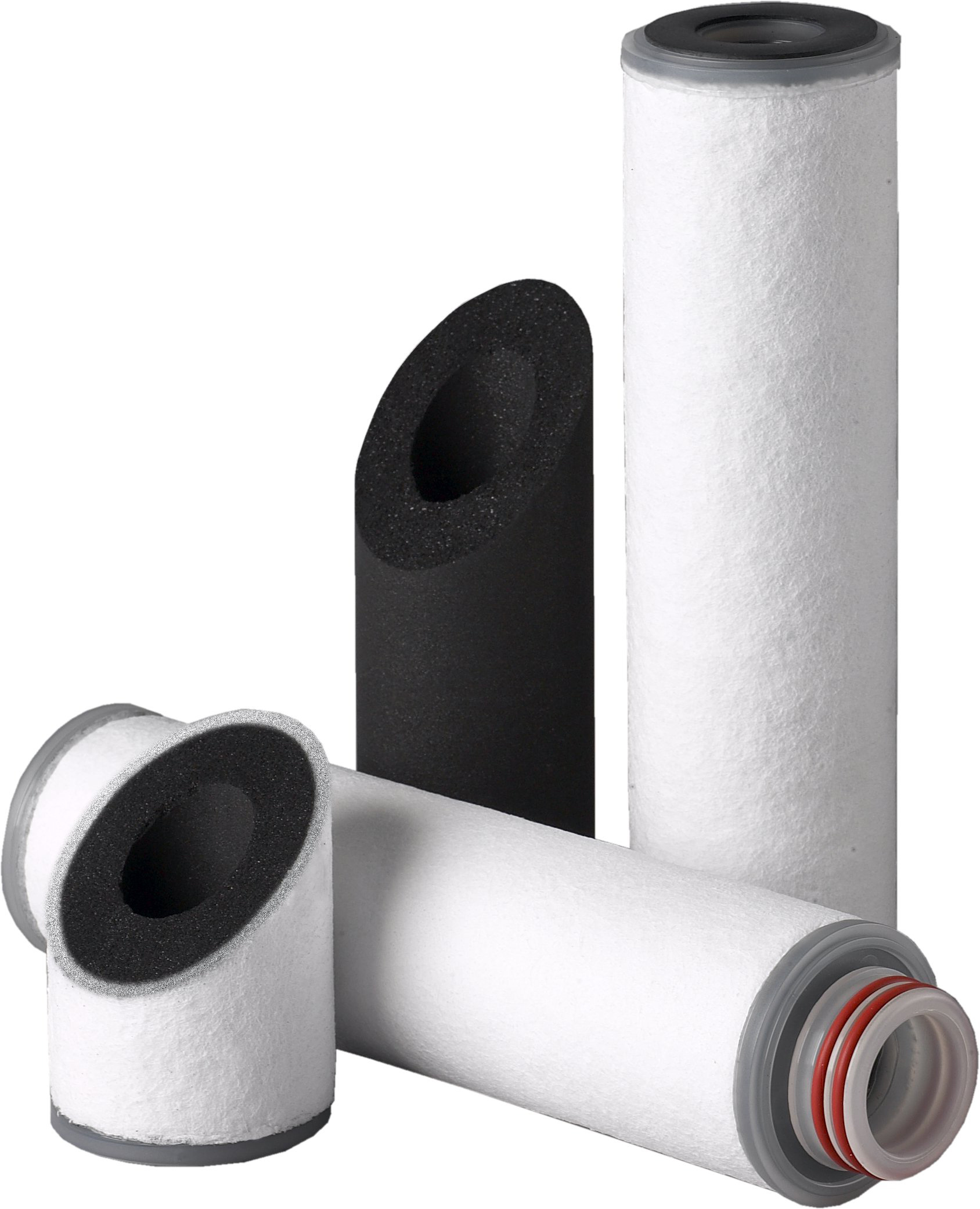
SupaCarb BP
Global Beer Producer
Water Quality Improvement
Australia
Improved and Guaranteed Beer Quality
Food & Beverage
Water has been quoted as 'the integrity and purity of beer'. The taste and appearance of a beer lives and dies by the quality of the ingredients used in the brew. As beer is approximately 90% water, its quality, or lack of it, can cause fundamental changes in its taste and aroma.
Municipal water is the most likely source of water for brewing. It undergoes rigorous treatment processes to ensure its safety for drinking. These processes often involve disinfection using chemicals such as chlorine to reach levels deemed safe for consumption. However, while these treatments make the water potable, they can react with the natural phenols present in the malt and hops during the brewing process. This reaction results in the generation of chlorophenols which can impart unwanted and unpalatable plastic like flavours and aromas on the beer.
The level of chemical treatment required can vary depending on the condition and length of distribution pipes as well as natural events such as flooding. For example, during floods, as water levels rise, additional contamination can enter the water source at reservoir or bore hole. Inevitably this leads to chlorine levels varying considerably over the year and seasons (wet/dry), providing significant challenges to the purification system in the brewery. Municipal water in the region of the brewery typically contained between 0.5-1.5ppm of chlorine.
Traditional carbon beds are often used to dechlorinate the water prior to being used in the brewing process. Here we discuss the successful implementation of cartridge filtration utilising carbon block technology.
The original brief for the project was to upgrade the existing MF (Microfiltration) modules with new chlorine resistant and more efficient UF (Ultrafiltration modules). However, the existing de-chlorination system used 3 large traditional granular activated carbon (GAC) beds housed in Glass Reinforced Plastic (GRP) vessels, installed prior to the MF stage as the membranes were not chlorine resistant. The opportunity was taken to also improve this stage.
This system had a number of problems associated with it:
The first stage of the process upgrade was to change over the old MF modules to a new 'state of the art', chlorine resistant UF plant. The plant was designed and installed by Amazon Filters distribution partner in the area, BHF Technologies who specialise in F&B processing technologies. Benefits of the system include:
The 3 GAC beds were replaced by SupaCarb BP carbon block cartridge filters. As the UF modules were chorine resistant the carbon stage was placed downstream of them. This configuration ensures excellent protection to the carbon stage, thus leaving the SupaCarb BP's to deal purely with reducing chlorine levels.
The SupaCarb BP is manufactured from a combination of both powdered and granular carbon providing excellent chlorine removal.
150 off 30" SupaCarb BP filter cartridges were installed across 6 stainless steel housings to cope with a total flowrate of 80m3/hr (see installation photo above).
The carbon stage was followed by 30 off 30" SupaPleat Plus particulate removal filter cartridges as a preventative measure should the carbon blocks be damaged due to out of trend process conditions. Damaged filters can result in carbon particles being released from the filter.
We'll make sure you're getting the best out of your filtration system